Ecommerce: Leveraging Supply Chain Tech...Where to Start?
- Webmaster
- Apr 14, 2020
- 6 min read
Create a blog post subtitle that summarizes your post in a few short, punchy sentences and entices your audience to continue reading.

A recent McKinsey study found that only 14% of digital transformations sustain the performance improvements they are designed to achieve. That is a staggeringly low number when you consider the pace at which the demand for digital solutions is spreading across business functions. When innovation is the mantra for your supply chain, where do you start innovating with technology and how do you become part of the 14% crowd? In this blog I share a path to becoming a "14 percenter" and contend it's rarely a bad call to start with a well-defined business problem (or "opportunity") to solve.
The Problem to Solve In business we encounter general business problems that keep the C-suite up at night and specific, related problems that are usually top of mind for functional leaders. In this blog we'll use the following example of general and specific problems:
General Business Problem: The COVID-19 pandemic has disrupted our consumer electronics business by shifting 15% of demand toward "social distancing" friendly online retailers. We can not survive a pandemic lasting longer than three months with our current business model.
Supply Chain (Specific) Problem: The immediate shift in demand has disrupted our flow of goods resulting in:
inadequate capacity for unplanned demand;
insufficient supply levels for new, high demand SKUs;
inability to confidently predict the breadth, depth, and duration of demand associated with the pandemic;
limited control over carrier costs, access, and performance; and,
an unclear plan to recover from the effects of the pandemic, assess likelihood of another pandemic, and transform.
We can assume the above problems are significant because it's fairly easy to imagine how they can impact a value stream like the example at Figure 1. However, by leveraging tools like impact mapping we can quantify the impact to be sure.

Design with Ease
“Do you have a design in mind for your blog? Whether you prefer a trendy postcard look or you’re going for a more editorial style blog - there’s a stunning layout for everyone.”
Figure 1. Example value stream
Once we've identified the problem and where the problem is showing up on our value stream we can identify the affected business processes.
The Opportunity Landscape
Let's take order fulfillment business processes at Figure 1 as an example; we'll focus onorder processing activitieswithinorder fulfillmentto illustrate how a technology solution can be used. First, we need to ensure order processing is mature enough to add technology. Figure 2 shows how we might look at process maturity.

Figure 2. Process maturity If order processing is standardized and measurable we can build performance factors into the design of a technology solution. If order processing is standardized, measurable, and optimizable we can plan for pending improvements and build our improvement approach into the design of the technology solution. This matters because who wants to design a technology solution to support several variations of the same process? Who wants to assume technical debt as soon as a technology solution is released because we didn't have an eye toward the future or didn't account for performance factors?
With a mature process we should be able to document:
what triggers the process;
how the process is accomplished;
who accomplishes what;
what tools are currently used;
what outputs the process produces; and,
how to determine whether the process is performing well or not.
At Figure 3 you see an example of order processing in a distribution center. The visual provides clarity regarding the process and context to see how changes to an activity might impact order processing as a whole. I like to highlight activities that are (or should be) enabled by technology to provide as much context as possible (see the blue outlines).
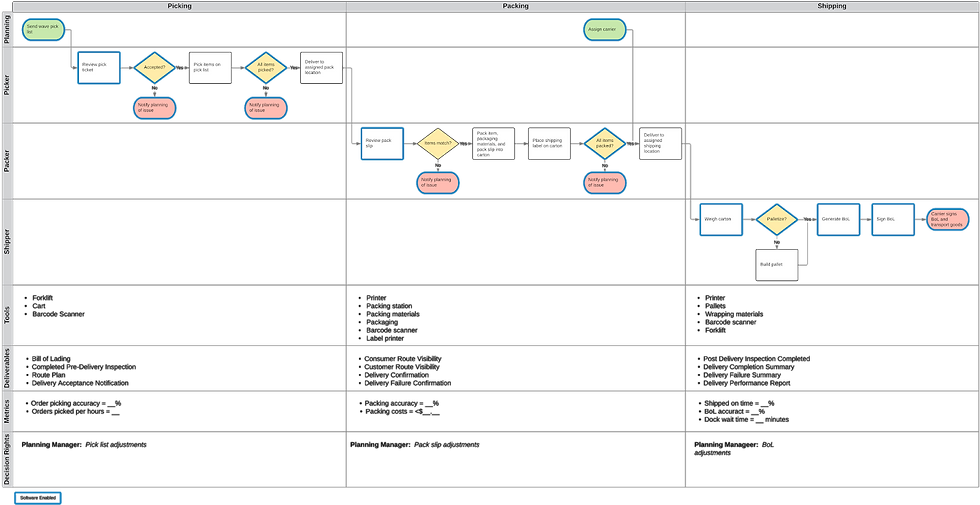
Figure 3. Example cross-functional process flow So far, we know why the process matters thanks to our value stream. We know how to deliver value because of our process flow. We know how well the process will be performed and what output we're trying to achieve from the process flow, as well.
After confirming we have a mature "enough" process to assess, let's determine whether technology is necessary and how much technology is needed to solve our problems.
The Solution
Through a process improvement event we learn that there are changes we should make to order processing to help address two of the five supply chain problems:
inadequate capacity for unplanned demand
insufficient supply levels for new, high demand SKUs
While we may find several opportunities to improve order processing, we prioritize opportunities that address our two supply chain problems. Figure 4 could represent our backlog of improvements; many of the improvements that solve our two supply chain problems sit above the green "cut" line.
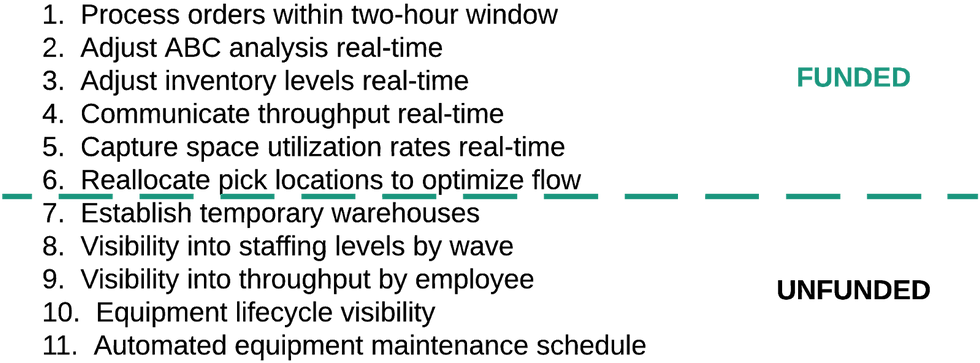
Figure 4. Improvement backlog example
After our process improvement event and based on the improvements we've selected we have aligned on a solution. We want to help solve our current space problem by optimizing utilization through dynamic order processing. Dynamic order processing allows us to shift the flow of goods as space and other factors dictate. Further, we want to help solve our supply levels problem by creating real-time visibility into order processing activities/impacts. Visibility helps upstream planning activities re-allocate available supply real-time, determine order fulfillment cycle time commitments, and other factors to help weather the pandemic.
Technology
After doing market research we learn there are warehouse management system features that might pair well with our list of funded improvements. So, we start the process of identifying the right features to use. Note that a technology solution may not be the overall solution, which we illustrate at Figure 5 (blue outline represents software-enabled functionality).
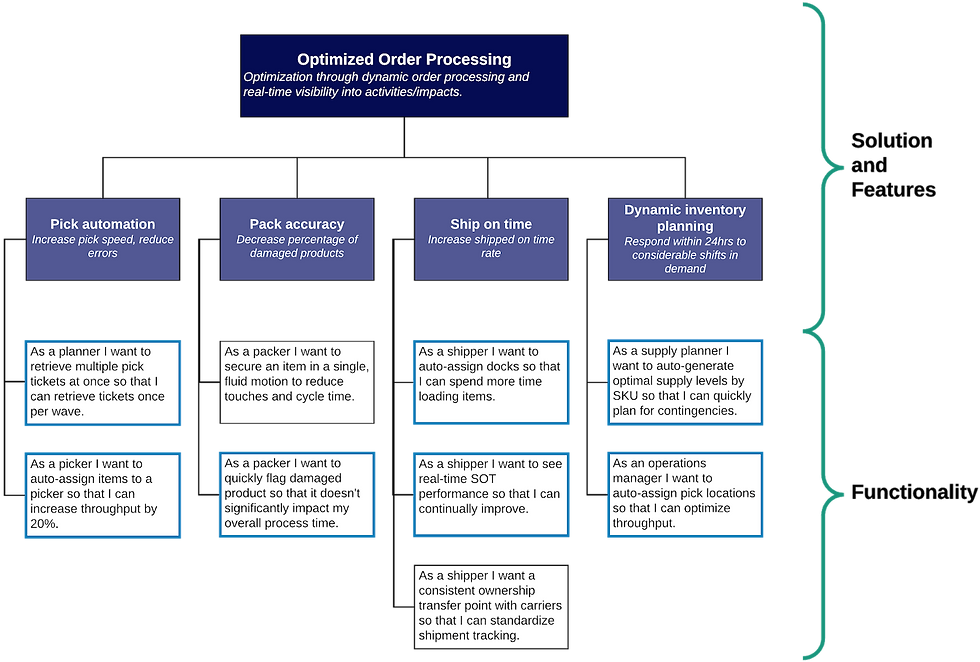
Figure 5. Features and functionality example Figure 5 shows how we might break down a solution into features and functionality. The goal here is to give our technology team enough information to develop, configure, or procure a technology solution that can be used to help solve our business problems. This is critical because we don't want to force our technology teams to make assumptions about how the supply chain works. At Figure 5 we highlight software-enabled functionality with a blue outline so that everyone involved can see how technology and non-technology functionality contributes to our overall solution. Further, we might consider using the three C's leveraged in Agile communities to provide additional insight to development teams. Card: The user stories shown at Figure 5 that show high level functionality for the user. Conversation: Provide a forum for technology teams to fully understand the desired functionality. Confirmation: Set clear outcomes the functionality should produce that the technology teams can incorporate in testing.
Lastly, we want to provide a timeline we can align on with the technology teams. I like to start with a simple roadmap (Figure 6) and get more detailed if it's necessary for decision-maker comfort or stakeholder alignment.
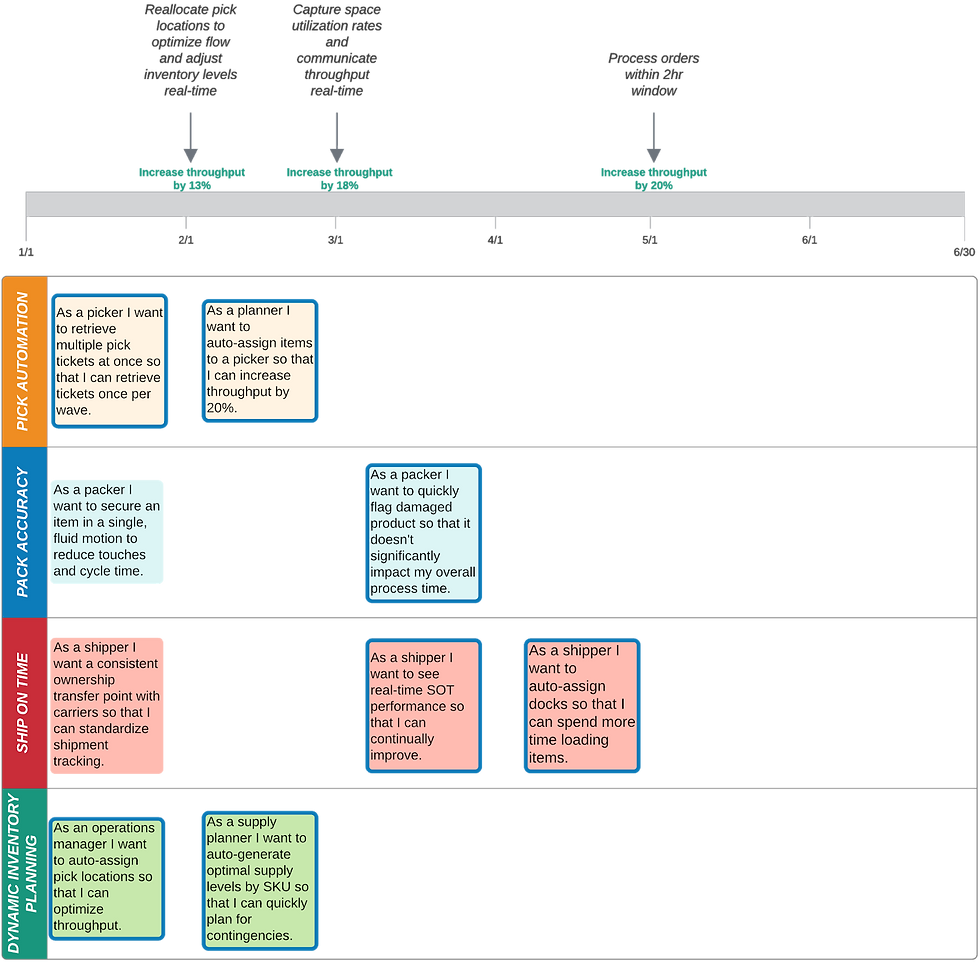
Figure 6. Example roadmap for optimized order processing solution.
Pulling it all Together
If I were to present our proposed technology to the supply chain leaders in our consumer electronics example, I would probably say:
"COVID-19 is disrupting our supply chain, specifically our ability to fulfill orders (Figure 1); we have a space and a supply problem. Increased demand for many C level SKUs has forced us to reevaluate our supply plan (Impact Map). Our metrics show that while we are able to process orders we are 20% slower to process orders with SKUs that are in high demand during this pandemic (Figure 2). Consequently, we reviewed order processing activities to find ways to improve throughput (Figure 3), and identified six improvements (Figure 4). We need dynamic order processing and real-time visibility into order processing activities to help solve our space and supply problem (Figure 5). We expect to improve order fulfillment cycle times by 20% (Impact Map) if we invest in the following enhancements to our warehouse management system that automate six pick-pack-ship activities to optimize space and two planning activities to improve supply levels (Figure 5). Current messaging indicates the pandemic will last five months and we expect to have the first wave of enhancements in place in one month (Figure 6), which will improve order fulfillment cycle times by 13% (Impact Map)."
Note that the example in this blog doesn't account for all of the problems and options to solve supply chain problems surfacing from a pandemic, but the approach laid out in this blog can scale up or down depending on the problem to solve.
As you entertain proposals for new technology, remember these key takeaways on your path to becoming a "14 percenter": start with a clear problem to solve; define what technology will enhance/enable; and recognize that a technology solution must help solve a real business problem to be a real solution.
Comments